Key Considerations During the Manufacturing of High-Quality Perforated Sheets
Source:www.cn-psp.cnAuthor:河北森驰公司 Last updated:2025-06-14 16:06:26 Browse:
Perforated sheets have become essential components in modern manufacturing, thanks to their excellent ventilation, light transmission, and decorative properties. They are widely used in architectural facades, machinery guards, filtration systems, furniture design, and many other industrial applications. However, producing high-quality perforated sheets is a complex process that demands attention to every detail. From raw material inspection to final surface treatment, every step directly influences the product’s performance and appearance. This article explores the key aspects that manufacturers must consider to ensure reliable and high-performance perforated metal sheets.
1. Comprehensive Material Inspection: Quality Begins at the Source
The performance of a perforated sheet starts with the raw material. Before any manufacturing begins, it's critical to inspect all aspects of the material, including type, thickness, tolerance, width, and length.
Using incorrect or substandard materials can lead to sheet deformation, cracking, or complete product failure after perforation. To prevent quality issues and ensure consistency, a strict incoming material inspection process should be established. This forms the foundation of a high-quality finished product.
2. Accurate Calculation of Hole Spacing and Edge Distance: Ensure Both Function and Aesthetics
During the punching phase, precision in calculating the distance between holes and between holes and sheet edges is vital. In large-scale or continuous perforation, any misalignment can result in asymmetric edges, making the sheet look unbalanced and affecting its installation and functionality.
Moreover, inconsistent spacing can lead to stress concentration in certain areas, reducing the structural integrity of the metal sheet. Therefore, precise blueprint design and proper parameter setting tailored to the application scenario are essential to avoid performance issues.
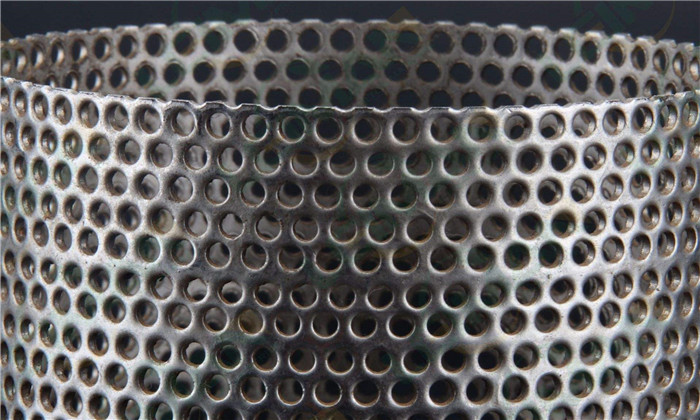
perforated sheets
3. Mold Inspection and Trial Production: Control Every Detail Before Mass Production
Molds are the heart of perforated sheet production. Their precision directly determines the accuracy of hole shapes, alignment, and whether burrs or misalignments occur. Before full-scale production, all molds must be thoroughly inspected for wear, distortion, or installation errors.
Conducting a trial production run with sample materials helps verify mold performance and allows timely correction of any deviations. This proactive step significantly reduces the risk of large-scale defects and ensures process stability.
4. Surface Flattening After Punching: Enhance Both Appearance and Usability
After the high-speed punching process, perforated sheets often experience slight warping or bending. If not flattened properly, this deformation can affect the sheet’s fitting accuracy, especially in precise applications such as ceilings, facades, and filters.
Thus, a dedicated flattening step is essential before the product leaves the factory. Using mechanical leveling equipment ensures the sheet’s surface is smooth and flat, which not only improves its appearance but also enhances assembly efficiency and operational reliability.
Conclusion
The production of high-quality perforated sheets involves a series of critical control points—from material selection and hole layout to mold calibration and final surface treatment. Each step must be handled with precision and care to ensure that the finished product meets both aesthetic and functional requirements.
For manufacturers striving to deliver excellence, continuous process optimization, investment in advanced equipment, and strict quality management are the keys to gaining a competitive edge in the market.