Perforated Metal Panel Materials: Types, Properties, and Applications
Source:www.cn-psp.cnAuthor:河北森驰公司 Last updated:2025-04-23 08:17:21 Browse:
Perforated metal panels (also known as punched plates) are functional decorative materials created by CNC precision punching machines that form uniform, regular hole patterns on various sheet surfaces, resulting in a mesh-like structure. Based on substrate properties, they can be categorized into:
Copper-based perforated panels: pure copper (C1100), brass (C1220)
PVC perforated panels: perforated polyvinyl chloride sheets
Nickel & specialty metal panels: pure nickel, nickel-based alloys, titanium alloys
Different perforated metal panel materials excel in strength, corrosion resistance, fire resistance, decoration, and thermal conductivity. Selection should consider project requirements, environmental conditions, and budget.
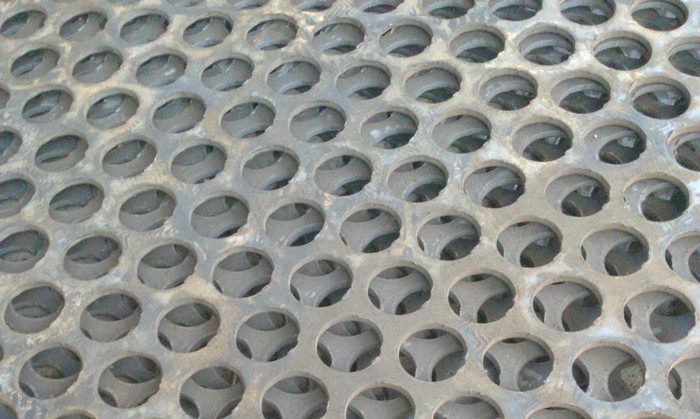
Iron Plate Perforated Metal
2. Iron-Based Perforated Panel Material Analysis
Cold-Rolled Steel
Properties: High strength and hardness; excellent surface flatness; strong coating adhesion; good heat resistance without deformation or discoloration at high temperatures.
Applications: Heavy machinery guards, industrial sieves, decorative screens.
Hot-Rolled Steel
Properties: Exceptional ductility; can be punched with large apertures; surface has minor scale requiring post-treatment; lower cost than cold-rolled.
Applications: Architectural partitions, safety stair treads, anti-slip plates.
Galvanized Steel
Properties: Zinc coating resists corrosion and rust; good formability without cracking; moderate price.
Applications: Outdoor railings, warehouse shelving, HVAC ducts.
Manganese Steel
Properties: Outstanding impact and wear resistance; high hardness; long service life; more challenging to process.
Applications: Mining screens, wear-resistant flooring, protective equipment.
Color-Coated Steel
Properties: Substrate usually galvanized or Al–Zn alloy; surface coated with PVC or baked enamel; customizable colors; corrosion-, fire-, and UV-resistant.
Applications: Curtain wall decoration, interior partitions, signboards.
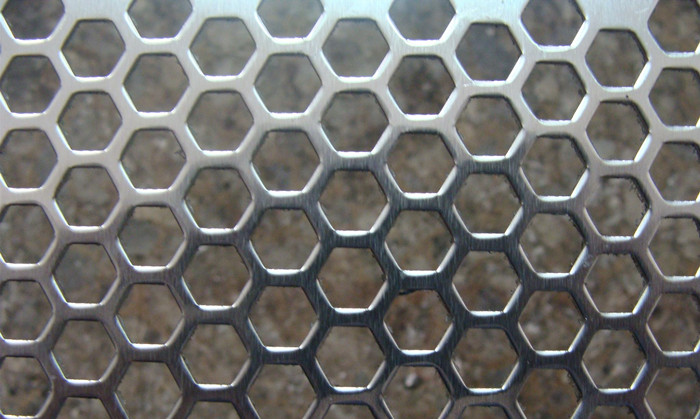
Aluminum Perforated Metal
3. Aluminum Alloy Perforated Panel Material Breakdown
Aluminum alloys are favored for their light weight, corrosion resistance, and recyclability, widely used in curtain walls, ceilings, and decorative screens. By series:
1000 Series (1050, 1060, 1100, etc.)
≥99% Al content; high purity; simple processing; economical; easily punched; ideal for indoor decoration, light partitions, and suspended ceilings.
2000 Series (2024, 2017, etc.)
High strength and hardness; common in aerospace; less used in routine architectural decoration.
3000 Series (3003, 3004, etc.)
Contains manganese; good corrosion resistance; suited for food equipment, chemical containers, and outdoor décor.
4000 Series (4043, 4032, etc.)
Silicon-containing alloys; heat- and wear-resistant; often used in welding wires and heat-resistant decorative components.
5000 Series (5052, 5083, etc.)
Magnesium-containing; excellent seawater corrosion resistance; superior tensile strength and ductility; widely used in shipbuilding, marine engineering, and vehicle manufacturing.
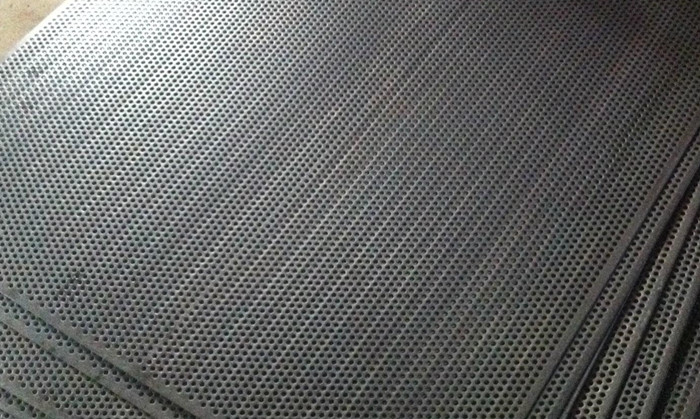
stainless steel perforated metal
4. Stainless Steel Perforated Panel Material Features
Stainless steel perforated panels combine high strength, corrosion resistance, high-temperature tolerance, and easy cleaning. Common grades and applications include:
201 Stainless Steel: Low cost; suitable for light indoor decoration and partitions.
304 Stainless Steel: Most popular; strong corrosion resistance; widely used in kitchens, bathrooms, and outdoor décor.
316/316L Stainless Steel: Contains molybdenum; better resistance to seawater and harsh chemicals; used in marine facilities and chemical plants.
430 Stainless Steel: Magnetic; good oxidation resistance; used in kitchen appliance panels.
409 Stainless Steel: High-temperature resistant and oxidation-proof; common in exhaust systems and industrial furnaces.
5. Copper, PVC, and Specialty Perforated Panels
Copper-Based Panels
Pure Copper (C1100): Excellent electrical and thermal conductivity; used for enclosures and heat sinks.
Brass (C1220): High hardness; can be plated in various colors; used for high-end décor and lighting fixtures.
PVC Perforated Panels
Properties: Lightweight; waterproof; insulating; customizable colors; easy to clean; eco-friendly.
Applications: Indoor ceilings, acoustic panels, exhibition displays.
Nickel & Specialty Metal Panels
Pure Nickel: High-temperature and corrosion resistance; chemically stable; used in chemical and electronics industries.
Nickel-Based & Titanium Alloys: Suitable for extreme environments like aerospace and medical devices.
6. How to Choose the Right Perforated Metal Panel Material
Functional Requirements: Determine corrosion resistance, fire resistance, sound insulation, or decoration needs.
Environment: Indoor vs. outdoor, humidity, chemical exposure, and temperature range.
Structural Strength: Load-bearing, impact resistance, or purely decorative.
Aesthetics: Surface finish, color, and gloss requirements.
Budget: From economical cold-rolled and galvanized steel to mid- to high-end aluminum, stainless steel, and copper alloys.
Post-Processing: Need for painting, brushing, plating, or other special treatments.
Choosing the right perforated metal panel materials requires balancing corrosion resistance, strength, longevity, aesthetics, and cost. We hope this guide provides a comprehensive reference for selecting “perforated metal panel materials” in architecture, industrial manufacturing, and other fields. For custom production or in-depth consultation, please feel free to contact us!